How to Do a Competitive Product Analysis: Evaluate Your Industry Position
Understanding your position in the industry is important to any successful business. That’s why it’s critical to ensure that you know how to do a competitive product analysis.
A competitive product analysis will help you to determine where you stand within your industry and what you need to do to outperform your competitors.
Performing this type of analysis is simple, but to make sure that you do it correctly, we’ve provided a list of steps that you should follow.
Understand Your Competition
Before conducting a competitive product analysis, there are a few things you need to consider. First, you must understand who your competitors are. Those selling similar products and services located within the same geographic areas are your direct competitors. These are the businesses you need focus on.
Start Your Research
Once you have a list of your direct competitors, you need to start your research. The best way to do this is to perform a professional market research study for each competitor. This helps you get to know the similar businesses in your industry so you can better market your company as the optimal choice for consumers.
To do this, gather information regarding the companies you’re competing against. How much are they selling their goods and services for? What makes consumers want to buy from them? What are some negatives about the company? These are just a few of the questions you need to answer while conducting your research.
Gather and Analyze Product Information Details
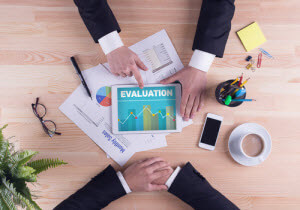
From there, you need to learn more about your competition’s products and services. We recommend reading their sales brochures, browsing their website and, if available, going over their annual reports.
These sources provide a wealth of helpful details. They show you how much other businesses are pricing their services and products for and gives you an idea of how well they’re performing to determine how you stand against your competition.
On top of that, these details will help you to understand the overall goals of other similar businesses, whether they’re looking to increase their market shares, maximize short- or long-term profits, or establish themselves as market leaders.
Develop Your Competitive Strategy
Use the information gathered in your research to create your competitive strategy. This should outline what you need to do to set your business apart from others and what you should do to market yourself as the better consumer option. For example, if you notice that your competitors are offering lower prices for their goods and services, you can lower your prices.
Your research details should also show you how your competitors are marketing their products and services. This information can help you to improve how you showcase your own selection to better meet your sales goals. Plus it can help you to improve your advertising efforts. For instance, you can enhance your website or social media presence if you notice that your competition doesn’t have a good online marketing campaign.
As soon as everything in your competitive strategy has been executed, you should see your business climbing higher within the industry.
Continue Your Research
However, doing a competitive product analysis right once isn’t enough. With new businesses forming every day, you’ll face more and more competitions.
With that said, you must continuously perform competitive research and improve your business strategies. This will help you to maintain your ranking within the industry and even help you to boost sales and production.
Performing a competitive product analysis is key to understanding your place in the industry and what you can do to improve your rank, so follow the steps above to give your business a better chance at success.
Read CPV Manufacturing’s blog for more business tips.