The Commercial Shutoff Valve
According to a report released by the Global Industrial Valves market, the market sales
for shutoff valves are expected to hit and surpass the $77 billion mark in the next three
years. The skyrocketing demand for these valves is a result of the rapid industrialization
that has been happening globally in the past decade.
A shutoff valve prevents flow in a system. But do you know how they work and what
could go wrong with them? Read this guide and understand the basics.
Types of Industrial Shutoff Valves
Shut off valves are an incredibly important part of any company involved in
manufacturing. These valves help regulate the flow of liquids and even gases.
Described herein are some of the basic valves that you can use in your industry.
Gate Valves
Also known as full-flow, on/off or isolation valves, they’ve been around for quite a long
time. Their popularity can be credited to their simple design, which significantly reduces
manufacturing costs.
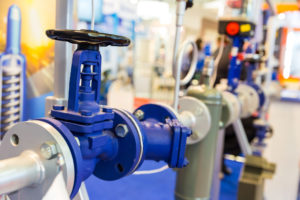
Just as the name suggests, gate valves are used to start or halt the flow of a fluid. They
achieve this through an internal gate which rises and lowers depending on the
movement of the circular knob on top of the valve.
Even though they make excellent valves, gate valves can’t function as throttling valves
as this tends to erode or wear them out. Gate valves are a common sight in process
industries due to their ability to withstand high temperature and pressure.
Ball Valves
Ball valves are different from other valves in that they use a ball instead of a gate to
control liquid flow. Due to this unique aspect, a ball valve can serve as an on/off valve
and at the same time can be used to regulate the fluid flow. Therefore, they’re more
common in the industrial sector than gate valves.
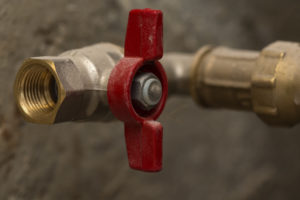
Other than that, ball valves can support high pressure and temperatures and also boast
a low-pressure drop. They’re also cost-effective, offer leak-proof services, and due to
their design can open and close quickly depending on the situation at hand. However,
even though they’re effective in liquid flow regulation, you can’t rely on them for
permanent throttling.
Butterfly Valves
Butterfly valves are also categorized under isolation valves. They derive their name
from their wing-like movement when in action. In recent years, there has been a
massive demand for these types of shutoff valves, especially in the oil, gas, and
automation industries.
This demand is attributed to the unique quarter-turn operation, which enables quick and
easy usage. These valves are also very accurate, which makes them even more useful
in the regulation of liquids and gases.
On top of that, they’re easy to install and require minimal maintenance. These features
make them even more prevalent in industrial applications.
Globe Valves
Globe valves offer excellent functionality for applications where frequent operation is
required or throttling of the flow is desired. The elongated flow path tends to allow a dampening effect, which is much different than the simple on/off operation of gate and
ball valves.
Globe valves tend to be easy to service and find favor in many chemical, fuel oil and
industrial gas applications. CPV has offered their O-SEAL®, Mark VIII®, and G-
Series® style of globe valves for many years and has decades of field-proven
performance to attest to the safety, reliability and ease of operation of the design.
Other Common Types of Valves Include:
- Stop Valves
- Check valves
- Relief or Safety valves
- Straight fixture shutoff valves
There are many other types of valves. Therefore, you should explore an extensive list to
choose what best suits your company.
Explore More Shutoff Valve Types
In a nutshell, there’re so many shutoff valves in the industrial realm today. Each shutoff
valve packs unique features which help improve the efficiency of your manufacturing
process. Check our page to learn more about shutoff valves and enjoy enhanced
efficiency today!