Flow Control Valve Checklist – Avoid These Common Errors
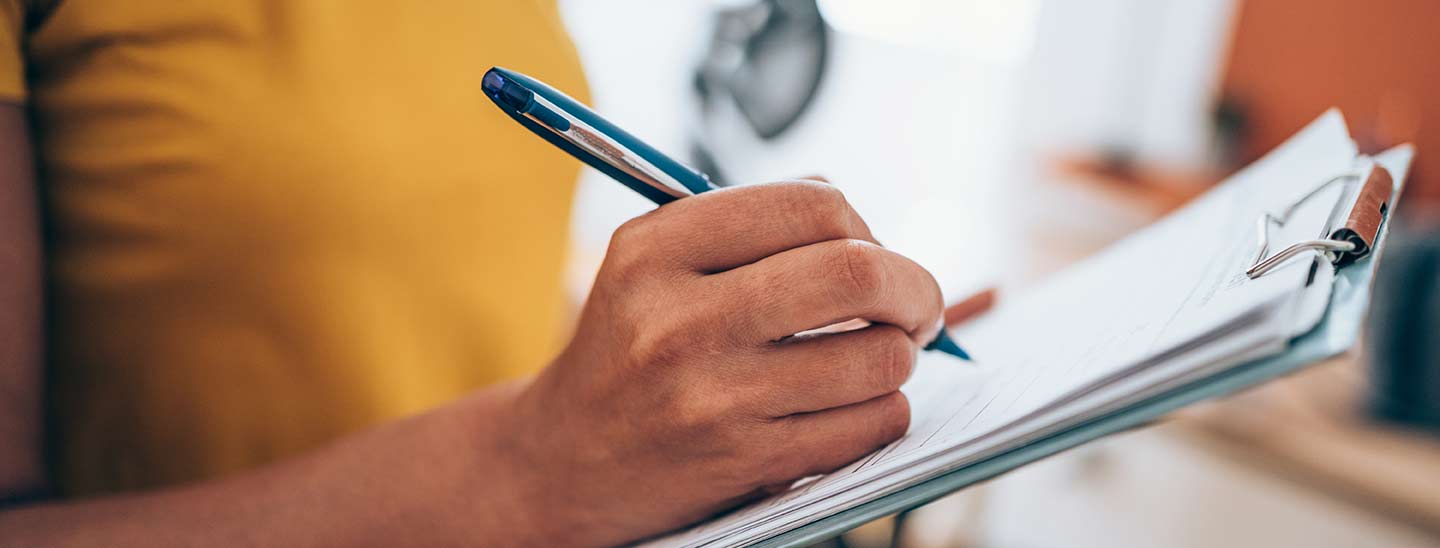
Selecting the right flow control valve for industrial gas or filling operations can help optimize performance, ensure safety and avoid the loss of tens of thousands of dollars in downtime or lost production. An extreme example was the Deepwater Horizon oil spill. According to the author of an article in New Scientist, within a list of eight contributing factors, one was valve failure—leading to a disaster that was responsible for billions of dollars’ worth of damage and immeasurable environmental devastation. There are certain variables engineers should consider, in order to avoid making mistakes when selecting or specifying flow control valves.
A few of the industries that rely most on flow control valves for gas filling operations would include:
- Chemical manufacturing–This is an industry that often requires precise control of gas flow during various stages of production and filling processes, to meter and regulate gas flow for chemical reactions, blending processes or packaging operations.
- Food and beverage industry—Processing for various product types relies on carbonation, modified atmosphere packaging or cryogenic freezing, with flow control valves ensuring the controlled release of the appropriate gases, such as carbon dioxide or nitrogen, which help maintain desired product characteristics, extend shelf life, ensure quality or are pivotal to product creation itself.
- Pharmaceutical and biotechnology—Precise gas control can help maintain sterile environments, control pressure differentials and/or regulate gas flow during filling and packaging processes, with precision necessary to maintain quality control or comply with regulatory standards.
Common miscalculations for flow control valves
Improper flow rate estimation. One of the most critical mistakes engineers can make is incorrectly estimating the required flow rate. Insufficient flow rate can lead to production inefficiencies, delays and even equipment failure. It is essential to consider factors such as gas properties, system requirements and potential future expansion when estimating the flow rate accurately.
Consult with the engineers at the valve supply company or manufacturer, look up relevant industry standards or utilize a simulation tool to help avoid this mistake.
Consider gas properties for compatibility
Different gases possess unique characteristics that can impact valve material selection. Gases can be temperature sensitive, reactive or corrosive, among other factors. An inexperienced engineer might not consider the entire list of characteristics when selecting a flow control valve, which can lead to material degradation or leakage. The consequences can include decreased system performance or increased safety risks.
Hydrochloric acid for example, is compatible with a variety of different fluoropolymers for soft goods such as O-rings, but only with one main metal, Hastelloy, for the valve itself.
The manufacturer can refer to material compatibility charts that supply important information to help match up materials with gas properties. This can help guide fabrication of the control valve.
Ignoring the pressure differential
This oversight can cause more than one issue:
- Inadequate flow rate: Engineers should pay attention to the required pressure drop as pressure differentials play an important role in determining the flow rate through a system. Ignoring this can result in an inadequate flow rate, causing inefficiencies or reduced system performance.
- Imbalanced system: The proper pressure differential helps maintain a balanced flow within a system. Ignoring this can disrupt the equilibrium and lead to uneven distribution of fluid or gases. This can create pressure fluctuations, backflows or erratic flow behavior, which if ignored for too long, can potentially damage system components.
- Increased expenditures: If a valve is not sized correctly and the pressure drops, the system must work harder to increase the pressure requiring more energy.
- Safety hazards: The system’s safety can be compromised if excessive pressure builds up downstream. This can increase leaks, or the risk of equipment failure.
- Inaccurate control: The valve may fail to provide the desired level of flow regulation, which can lead to inconsistencies in fill rates, instability or the system’s inability to meet required operating conditions.
Disregarding maintenance
A flow control valve, like other mechanical components, will require occasional, but regular maintenance to help it reach its potential for lifespan. It is important not to neglect routine inspections, or the occasional lubrication that can benefit a flow control valve. Doing so can help improve valve efficiencies and avoid malfunctions or unexpected downtime.
More often than a complete valve replacement, typically the soft goods can be replaced to provide extended life to the valve itself. In an existing application, CPV Manufacturing has provided upgraded valves. For example, an older style valve regulating oxygen flow for 15 or 20 years formerly was made of bronze. This style is being phased out of service and replaced with brass—an easy slip in/slip out replacement for fit, form and function.
Like any other task, selecting the right flow control valve for industrial gas applications requires attention to detail and when in doubt, consultation with the valve manufacturer. Engineers can avoid many of the common mistakes associated with valve malfunctions by paying attention to pressure differentials and gas properties, among other aspects. This can improve system performance, operational efficiencies and plant safety with a valve that operates faithfully for many years without interruption.
CPV Manufacturing operates its domestic manufacturing facility to fabricate the highest quality valves such as flow control valves. It has supplied valves that meet stringent standards within the U.S. Navy as well as components for the aeronautics industry and gas processing operations of all types. Learn more about our product line and view our valve selection or call to speak with one of our engineers.