How CPV Instrument Fittings Supply Secure, Long-Lasting Connections
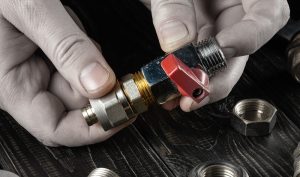
Reliable instrumentation connections are critical for system monitoring and control in processing facilities and in maritime, energy and aerospace applications. While traditional piping systems serve their purpose for main process lines, more delicate operations require the accuracy and information supplied by the proper fittings for applications that require data input.
Operators can rely on specially designed instrument fittings, which, when connected, allow transmission of accurate, real-time data about critical process measurements such as temperature, pressure flow and level. Data flow enabled by these instrument fittings enables operators to make informed decisions. Think of these connections serving as the nervous system of a processing facility, enabling proper control responses, safety system functions and quality control measures.
Understanding Instrumentation Fittings
Instrument fittings are specialized connectors designed for smaller diameter tubing systems, typically in the quarter-inch range, rather than larger process piping. These fittings derive their name from their primary function linking process equipment and monitoring instruments, enabling essential system verification and calibration functions.
Key Selection Factors
When choosing instrument fittings for industrial applications, several factors require careful consideration, including:
- Media Compatibility: The type of fluid or gas flowing through the system determines material selection and sealing requirements
- Operating Parameters: Pressure and temperature requirements vary and help determine fitting compatibility
- Material Selection: Compatibility between pipe and fitting materials is essential for system integrity
- Sealing Mechanism: Different applications may require specific sealing approaches
- Application Requirements: The specific use case will influence fitting choice
- Budget Considerations: Initial costs must be balanced against long-term reliability
The Hidden Costs of Unreliable Instrumentation Fittings
Unreliable instrumentation connections can lead to a host of problems that can cost facilities time and money. The problems can include:
- False readings leading to incorrect control actions
- Delayed or missed alarm conditions that could compromise safety
- Process upsets due to inaccurate feedback to control loops
- Product quality issues from imprecise measurements
- Equipment damage from undetected abnormal conditions
- Increased maintenance costs from troubleshooting and repairs
- Energy inefficiency from poor process control
Available Fitting Solutions
CPV offers multiple fitting solutions for use with our Instrument Valves that address these requirements and meet or exceed quality and performance standards:
- Traditional compression connections with ferrules
- Advanced O-Ring Face Seal (ORFS) fittings and Adapters for various connection types
Each style can provide reliable connections depending on the application and specifications, however, the ORFS design represents a more sophisticated, advanced form of fitting technology, offering enhanced adaptability and performance in demanding applications.
Military-Grade Performance
What sets CPV’s instrument fittings and valves apart is their proven performance in military applications, particularly in naval vessels and submarines. These fittings and valves meet rigorous military standards for shock and vibration resistance (MIL-S-901, MIL-STD-167), ensuring reliability even under extreme conditions. This military-grade durability translates directly to superior performance in harsh conditions that might be encountered in industrial applications.
Applications and Advantages
In processing facilities, instrument fittings play multiple critical roles in system monitoring and control. Their primary functions include:
- verifying system pressure
- monitoring temperature variations
- measuring flow rates
Instrument fittings also serve as essential access points for calibration procedures and provide necessary bypass connections for system maintenance.
The compact design of instrument tubing systems offers significant advantages over traditional piping approaches. Installation costs are substantially reduced due to simplified routing and fewer connection points. This streamlined design not only minimizes potential leak paths but also provides easier access for maintenance personnel. Instrument fittings, typically smaller in size, allow for better utilization of facility space and allow easy access for system modifications when necessary.
Low-Maintenance Design Features
Many facilities struggle with a maintenance crew already stretched thin, with more tasks than there is time in the day. CPV’s commitment to low-maintenance performance is evident in three key design elements.
First, their ORFS (O-Ring Face Seal) technology represents a significant advancement in fitting design. This innovative approach enhances sealing capability while reducing the risk of connection failure. The ORFS design also provides superior resistance to vibration and adapts more readily to various connection types.
The second key feature is the ¾ turn operation mechanism of our Instrument Valves. This design choice significantly reduces maintenance time while minimizing wear on sealing surfaces. Technicians appreciate the simplified operation, which contributes to more efficient maintenance procedures and reduced system downtime.
Premium materials form the third cornerstone of CPV’s design philosophy. Their corrosion-resistant construction ensures longevity in harsh environmental conditions. These carefully selected materials contribute to an extended service life, particularly important in demanding applications or harsh environments.
Critical Industries and Applications
CPV’s instrument fittings have evolved beyond their naval origins to offer durable performance across several demanding industries. Possibilities include the defense and shipbuilding sector, military support vessels or shipyard testing facilities, the aerospace industry for fluid system monitoring, or the energy sector. Each could benefit from the corrosion resistant material, precision, MIL grade standards and low-maintenance features.
Industrial processing represents another key market, with applications potential in chemical and petrochemical facilities. The fittings’ robust design makes them ideal for industrial gas handling and critical fluid control systems, to protect system integrity and enhance operational safety.
Looking Forward
As industrial processes become increasingly automated and monitored, the role of reliable instrumentation connections increases in importance. CPV’s commitment to providing high-quality, low-maintenance fitting solutions ensures that facilities can maintain efficient operations while minimizing labor requirements and system downtime.
For processing facilities seeking to optimize their instrumentation systems, CPV’s range of instrument fittings and valves offers a proven solution that combines military-grade reliability with practical industrial functionality. The resulting operational efficiency and cost savings make them an ideal choice for industries where performance and reliability directly impact the bottom line.
Visit our website or download a catalog for more information about our instrumentation connections and valve options.