Top Considerations When Selecting a High-Pressure Relief Valve
High-pressure relief valves fulfill a critical safety function in multiple applications, ranging from petrochemical to power, marine and aerospace industries. Regardless of the application, certain primary features can help guide engineers when selecting a durable high-pressure relief valve that will help avoid catastrophic failure to protect your workers’ health and safety while also preserving capital equipment.
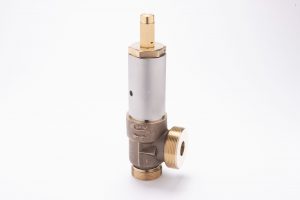
What’s the Primary Purpose of a Relief Valve?
A relief valve functions as an operational safety feature, to help control and regulate the flow of high-pressure fluids and gases. It is designed to vent off extra pressure, whether from gas or a liquid. The design triggers the valve to open once a system reaches a predetermined set pressure.
This protects systems from experiencing pressures that exceed their design limits. Once a system reaches that predetermined level or valve set pressure, the relief valve opens, and a portion of the liquid or gas is removed from the system by diverting it through an outlet in the valve.
The relief valve helps maintain safe pressure levels to prevent potential damage or catastrophic failure. Once system pressure drops to its predetermined normal level, the relief valve closes or “reseats” until it is needed again. While a relief valve functions as a safety feature, it differs from a safety valve which only triggers in an emergency.
A safety valve opens instantly to its full venting capacity while a high-pressure relief valve opens gradually when system pressure reaches the preset level.
A catastrophic failure could mean loss of capital equipment such as pipes if the pressure doesn’t diminish. Pressure build up, if unrelieved, can lead to more serious consequences such as an explosion, potentially harming personnel and causing more widespread damage to equipment and surroundings.
High-pressure relief valves are found in several different industries including marine applications on naval and commercial vessels, aerospace, industrial gas, the petrochemical industry, power plants and many industrial applications as well.
Factors for Specifying a Relief Valve
There are several factors to take into consideration when specifying a relief valve. These can include:
1. Set pressure limit
The set pressure limit is the threshold that triggers the high-pressure relief valve action. For example, if the normal system pressure is 3000 PSI the engineer might determine the set pressure limit is 3300 PSI. Once pressure reaches that threshold it triggers the relief valve which then vents the excess liquid or gas. Consistent triggering of the relief valve often indicates a problem with the system.
2. Valve capacity
This relates to the amount of flow the valve is able to relieve.
Connection size and type—The connection of the valve or valve size needs to correspond to the size of the discharge piping. Operators must also determine the connection type for the inlet and outlet ends, typically threaded or flanged.
3. Shock and vibration
Material selection, design and testing will reveal the ability of the valve to withstand shock and vibration without triggering its action. Naval vessels require parts such as relief valves pass specifications for shock and vibration.
4. Environment
This particularly plays a role in material selection for the valve construction when it will come into contact with a corrosive or abrasive substance. An example of this would be a marine relief valve that can or will regularly encounter salt water. All CPV Mfg. high-pressure relief valve specified for marine purposes are manufactured of bronze.
5. Temperature
This factor impacts O-ring material selection. Depending on the temperature range, CPV can specify a specialty elastomer or material for the O-ring.
6. Orifice size
This relates to the relief capacity of the valve. When the orifice size is smaller, the relief valve can rate to a higher pressure but relieve less capacity. The larger the orifice, the lower the pressure but the higher the relief capacity of the valve.
7. Positive Reseating
All relief valves manufactured by CPV have a positive reseating, which means after it blows at pressure, it reseats itself or reseals once the pressure drops into the normal range. This reseating capability allows for continuous operations. Look for a soft seating design which acts as a bubble tight seal, versus a metal-to-metal interface, which can be prone to leaking.
8. Spring adjustment
A sensitive spring, such as those incorporated into a CPV high-pressure relief valve, allows the operator to adjust the release for a very narrow PSI range. For example, the spring itself might be rated for 1,000 to 2,000 PSI, but the sensitivity enables the operator to set it at a specific target, such as 1,015 PSI, for example.
Add to this testing capabilities, and the cooperative efforts of the engineering design team and the valve manufacturer can produce a valve with the most accurate control of the blowdown pressure setting.
Why Choose CPV Manufacturing?
CPV manufactures relief valves in two different series: the 150 series and our flagship O-SEAL® line. The 150 series is a line of soft-seated female threaded relief valves with set pressures that range from the low end of 5 PSI up to 300 PSI.
The O-SEAL® line of soft-seated valves and separable fittings allow for positive control of high-pressure liquids and gases. This line offers leak proof performance from vacuum up to 6000 PSI (414 bar).
CPV has been supplying high-pressure relief valves to the U.S. Navy for mission critical applications since the 1950s. Each individual valve built by CPV Manufacturing undergoes testing, not random or batch testing, but each valve.
Valves must meet a safety factor for the pressure rating of four to one. If a valve is rated for 6,000 PSI for example, the valve strength is up to or in excess of 24,000 PSI. In addition, all valves meet the ASME Boiler and Pressure Vessel Code. Our valves are over-engineered to exceed the pressure strength rating, for the utmost in reliability.
Trust CPV Manufacturing for durable, reliable, high-pressure valves that meet the stringent requirements of the U.S. Navy, found in service in submarines, aircraft carries and other vessels throughout the fleet. We can work within your specifications or consult for customized projects and applications.
Contact us today for a quotation.